Good at【Hi-mix Low-volume】connection soulution
Feel the customer’s expectations with heart,think of solutions with brain
Manufacturing of Wire Harnesses
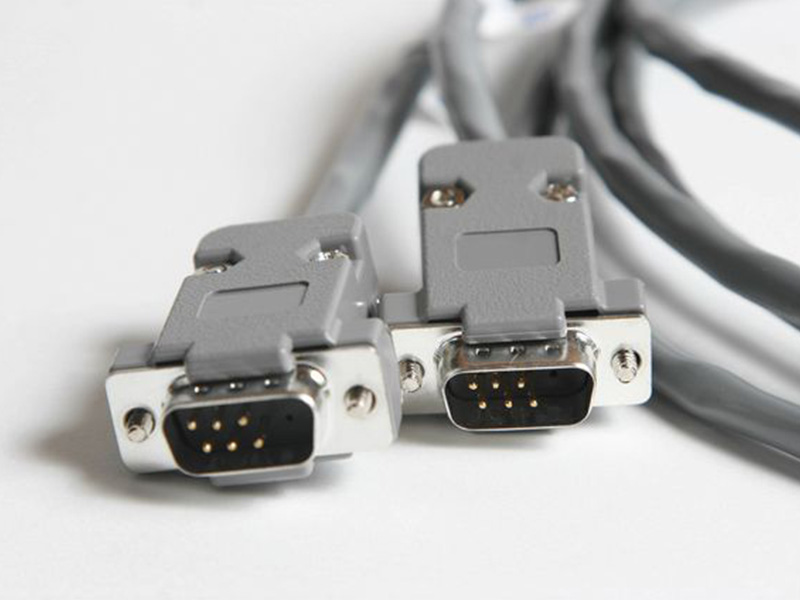
Engineering Capability
We have participated in the research and optimization processes of wire harnesses for over 500 different types of equipment in fields such as power quality, medical equipment, scientific instruments, semiconductor equipment, high-end manufacturing, rail transportation, special machinery, mining, and oil & gas. Fully understanding the application requirements for wire harnesses in these fields, we assist customers in VAVE, standardization, and optimization list construction for wire harnesses and their main raw materials (namely connectors and wires). With rich professional experience in designing and optimizing connection solutions for our customers, we have achieved the economy and accessibility of raw materials on the premise of ensuring the functional performance of our products, thereby improving the assemblability, testability, reliability, accessibility, and cost-effectiveness of wire harnesses.
Delivery Capability
We have established a structured process document system and accumulated a rich process knowledge base. With the assistance of the CAPP system, we have realized the inheritance of experience and economically and quickly formulated correct, clear, and detailed special SOPs for each wire harness product, ensuring that SOPs are available for “high-mix low-volume” wire harnesses, just as they are for high-volume wire harnesses.
Mastering nearly 80 processes for manufacturing the wire harnesses commonly required in the industrial and medical fields, we are capable of pressing 32 AWG terminals to 5’0 wires. We adopt a variety of welding methods such as the constant temperature soldering iron, semi-automatic welding machine, Hotbar welding machine, and ultrasonic welding. We use injection molding processes for plastic materials such as PE, PVC, and TPU, and employ transfer printing, sleeve printing, label printing, and other sign-processing methods. We have established a laboratory that covers the full performance of wire harnesses and can continuously provide our customers with high-quality and efficient “one-stop” wire harness manufacturing services.
In response to the low volumes and frequent changeovers of wires in production of “high-mix low-volume” wire harnesses, we implement lean production to improve operational efficiency through specialized lean units. By cultivating multi-skilled workers and conducting performance evaluations within lean teams, we address imbalance and waste in the wire harness production process. We ensure the quality of our wire harnesses through job qualification management, downtime mechanism, and comprehensive quality management involving all staff. Through miniaturization, multifunctionalization, and fool-proofing measures for equipment, we solved the problem of quick wire change and gained the ability to provide JIT delivery to our customers with high efficiency, high quality, and high flexibility.
We practice PDCA closed-loop management and continuously strive for higher quality and efficiency.